Angry Panda Factory
Mazda FD RX7 FD3S Carbon Fiber Side skirt (type F)
Mazda FD RX7 FD3S Carbon Fiber Side skirt (type F)
Couldn't load pickup availability
Made using the vacuum injection method on twill Torai Carbon fibre. This pair of skirts is made strong and light, only (800g) using UV resistant epoxy resin which reduces fading from exposure to the element. The vacuum injected process makes the part crack and shatter resistant.
Vacuum-infused carbon fiber, also known as vacuum resin infusion or vacuum-assisted resin transfer molding (VARTM), is a manufacturing process used to produce high-quality carbon fiber composite parts. Here's how the process works and some of its advantages:
-
Improved Quality: Vacuum infusion ensures thorough resin impregnation throughout the carbon fiber layup, resulting in a higher quality and more consistent finished product. This process helps minimize voids, resin-rich areas, and other defects commonly associated with traditional hand layup methods.
-
Better Fiber Alignment: The vacuum pressure helps compress the carbon fiber layers, ensuring better fiber alignment and consolidation. This leads to enhanced mechanical properties, such as higher strength, stiffness, and fatigue resistance.
-
Reduced Weight: Vacuum infusion allows for precise control over the resin-to-fiber ratio, optimizing material usage and reducing excess resin content. As a result, vacuum-infused carbon fiber parts tend to be lighter in weight compared to parts produced using other manufacturing techniques.
-
Complex Geometry: Vacuum infusion is well-suited for producing parts with complex shapes and intricate details. The process can accommodate complex molds and intricate fiber orientations, allowing for the production of highly customized and aerodynamically optimized components.
Share

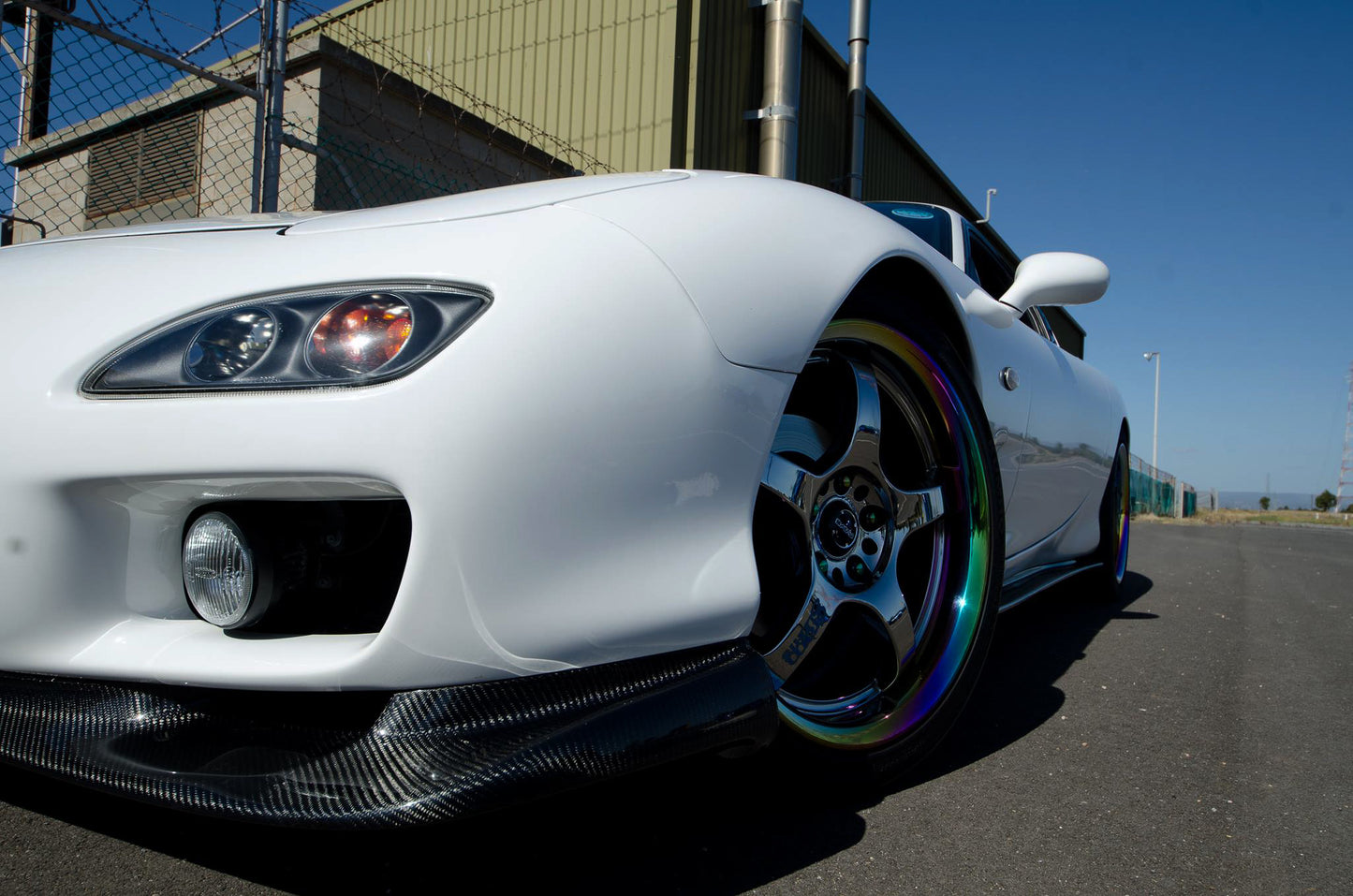
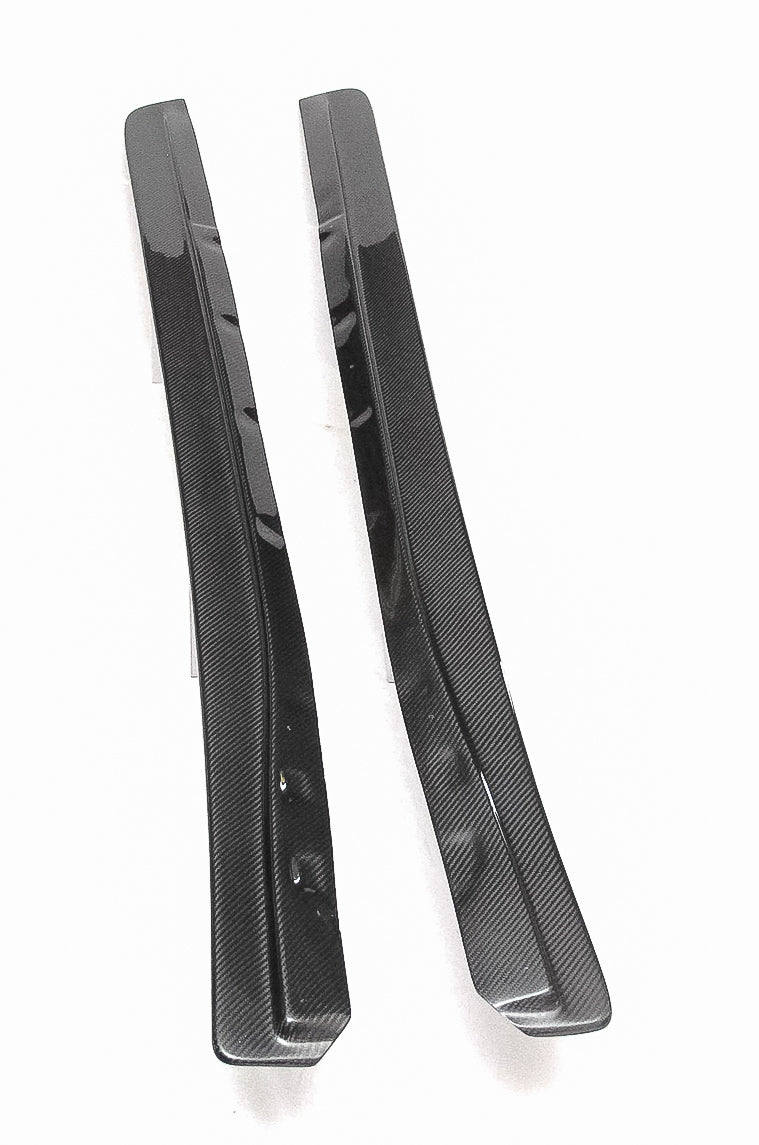
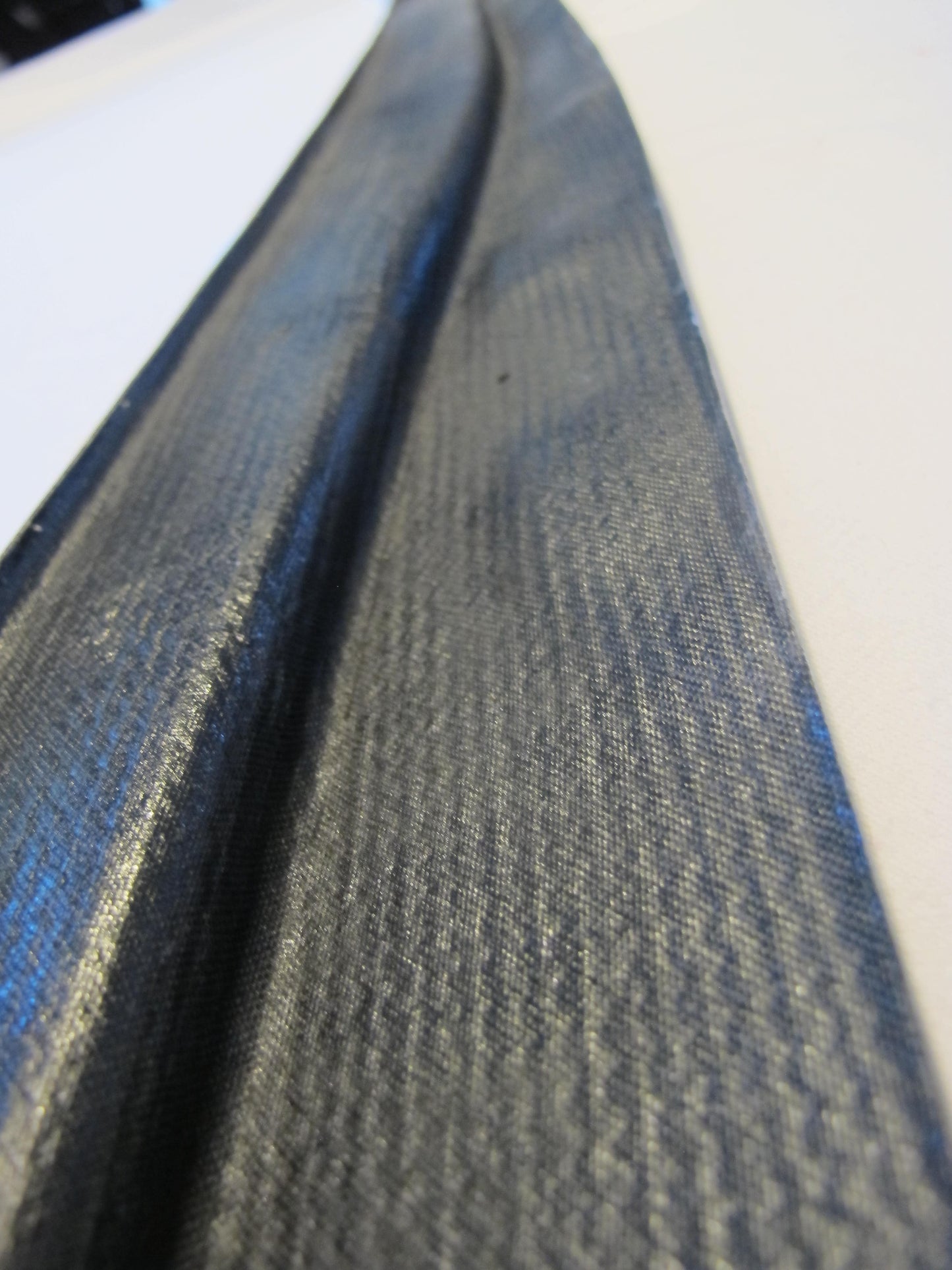